Five ways 5G unlocks IoT in Industry 4.0 – and three places to do it (Reader Forum)
Advances in automation have impacted every industry, but arguably none more so than the manufacturing sector. Traditional assembly lines are being replaced by intelligent factories where machines not only handle assembly but help optimise resources and drive down costs. This technology revolution, known as Industry 4.0, is becoming a reality thanks in no small part to the industrial internet-of-things (IIoT) and availability of 5G private networks.
By 2029, the Industry 4.0 market is expected to be worth $377.3 billion. Machines, robots, sensors, people, and drones all require seamless connectivity in IIoT. Previous generations of wireless networks could not support these massive communication needs, which is why 5G is pivotal for Industry 4.0. Not only does 5G enhance connectivity, it offers several benefits that are fuelling this Industry 4.0 revolution. These include:
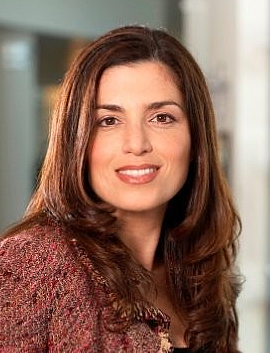
1 | Faster data speeds and higher bandwidth
5G provides data transfer rates of up to 20 Gbps, more than 20 times faster than 4G. This enables the rapid transmission of large volumes of data from devices, machines, and sensors in industrial environments.
2 | Extremely low latency
With latency as low as 1 millisecond, 5G enables IIoT technologies to communicate with unparalleled speed. Imagine the benefits of monitoring production lines, machines, and equipment in real-time.
3 | Improved reliability and availability
Connectivity disruptions are an accepted part of previous generations of wireless networks. However, 5G supports consistent connectivity even in remote industrial environments.
4 | Enhanced edge computing capabilities
5G can be combined with edge computing to facilitate data processing and analysis at or close to the source, supporting real-time decision-making for IIoT systems.
5 | Massive device connectivity
The latest generation of wireless technology can simultaneously support up to one million connected IoT devices, sensors, and robots, which is vital given Industry 4.0’s technical complexity.
The combined benefits, enabled by these technology features, are paving the way for a variety of new Industry 4.0 use cases. This include:
1 | Smart warehouses
The high bandwidth afforded by 5G enables warehouses to support large, distributed networks with numerous connected devices and sensors for enhanced inventory management and process optimisation. In addition, 5G’s ultra-low latency means inventory tracking, machine control, robot operation, and other data-intensive tasks have real-time processing and communication capabilities. This improves productivity, reduces labour costs, and ensures more reliable warehouse communications.
2 | Predictive maintenance
Another benefit of 5G is the ability to predict equipment failures and proactively address issues before they impact operations. Predictive maintenance prevents downtime and extends the lifespan of machines. Additionally, manufacturers can make fine-tuned adjustments by continuously monitoring machine health to maintain production standards.
3 | Flexible manufacturing
5G provides greater flexibility in the manufacturing process. Robots and drones aren’t restricted by connection issues, making materials-handling and logistics more agile. As the technology matures, it will provide a vital link between factories and the market – enabling manufacturers to respond to changing demands or external logistics challenges efficiently.
The ability to collect, analyse, and actualise data in real-time is crucial for Industry 4.0. Armed with this intelligence, manufacturers can make real-time adjustments to address quality issues, inefficiencies, and safety concerns, accelerating production processes and lowering costs.
Testing with digital twins
5G is pivotal to realising Industry 4.0’s potential. However, these capabilities must be tested to ensure they work as expected and this requires incorporating digital twins. These virtual models of physical systems draw on data from sensors and other sources to create an emulation that tests how the system will behave under different conditions. This allows manufacturers to evaluate 5G infrastructure, examine use cases, and determine the best way to integrate the network.
For example, engineers can use the simulation to evaluate the optimal configuration of machines, sensors, and robots, identify potential bottlenecks that may occur during periods of high production, and implement a plan to avoid that scenario. Digital twins and 5G are already fuelling Industry 4.0 innovations, and this will only multiply as adoption increases.
With 5G, smart factories will become a reality, enabling an array of innovative manufacturing concepts that will enhance productivity and efficiency. Advances in augmented reality will open up new possibilities for remotely accessing and troubleshooting manufacturing equipment, with real-time overlays to guide the complex process. Expect to see these use cases and many more as the industrial revolution accelerates, with 5G capabilities the key to unlocking Industry 4.0.
Comments are closed.