‘It’s all about speed’—Georgia-Pacific on gen AI at the industrial edge
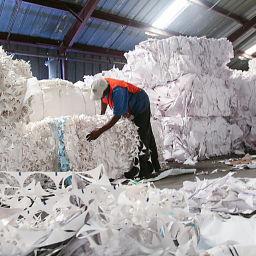
Like virtually every other large global enterprise, paper product manufacturer and distributor Georgia-Pacific is working to leverage generative artificial intelligence (gen AI) for workforce productivity gains. While the current focus is “all about speed these days,” according to Vice President of Innovation Michael Carroll, the underlying problem dates back to the 2000s when manufacturing productivity increases began to slow then plateau as skilled workers began exiting the workforce en masse which was met with a scramble to replace institutional memory with technology.
At the time, Carroll said, “You could start to feel this difficulty in being able to sustain productivity…which made automation appear.” But this led to an overcorrection that ultimately saw frontline workers distracted by an overload of information and analytics that were meant to augment human knowledge. The cumulative effect of these distractions, this “generational susceptibility” to distractions, was the opposite of the intent—instead of workers using technology, instead of knowledge, to become more productive, the opposite happened. Then COVID-19 hit further compounding the problem around knowledge loss and generational susceptibility.
Carroll said that at its core, gen AI is a technology that lets people interact with other technologies; it makes knowledge that exists in silos within a company something that can be harvested and used for decision making. It’s all about communicating contextualized information to a worker when and where it’s needed.
He referenced the Purdue Model, a reference enterprise architecture that follows a six-level hierarchical model. To recap:
- Level 0 is the physical process, including sensors, actuators and other devices on the factory floor.
- Level 1 refers to basic control—things like programmable logic controllers and remote terminals that directly manage physical processes.
- Level 2 is all about monitoring and supervising process control systems; this is your first level of data aggregation and attendant visualization.
- Level 3 is the manufacturing operations systems that handles the overall operation of the manufacturing process, including scheduling, batch management and quality control.
- Level 4 gets into business planning and logistics wherein manufacturing operations are integrating with the manufacturer’s larger business.
- Level 5 is the enterprise network and covers everything from corporate IT and finance to human resources and company-wide applications.
Right now, Carroll said, humans serve as the intermediaries between those levels and create something of a “learning loop” that informs decision making. “Now what we’re really trying to get at is how do I build artificial intelligence that converts that human learning loop…to a digital learning loop that is agent based?” This future state would create transparency between these layers in terms of understanding the fundamental inputs into thought and reasoning processes that result in the larger output of intelligent decision making. “Everything is explainable all the way back through your generative AI model which is taught by your employees.”
Carroll continued: “In this agent world, you have to be able to deliver to the employee what do you need to know, what do you need to do with it, and when do you need to do it?…You have to be good at the ability to deliver content to the individual relative to what their persona says they’re trying to achieve…The disappointing part is that today you have to build this world yourself. There are no applications that allow you to go do this. Hopefully in the future there will be a platform that agents can live in.”
While acknowledging all of the point solutions he sees vendors putting into the market, Carroll said, “The issue is the orchestration of your problems and getting those delivered contextually and prioritized to the frontline when they need to get there…You have to become your own orchestrator of context.”
Comments are closed.